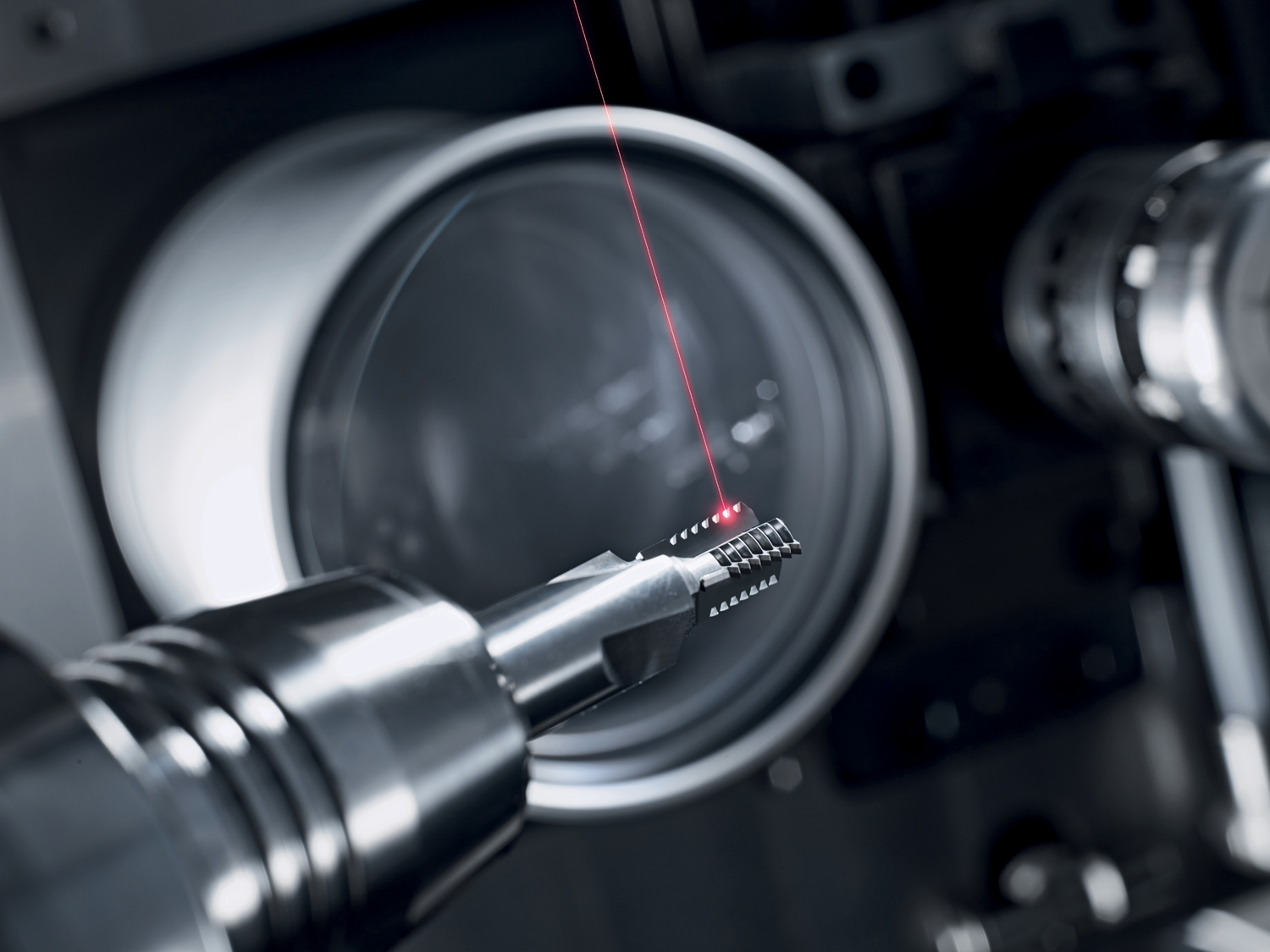
Micromachining and Microprocessing
Micromachining encompasses highly diverse tasks such as drilling, engraving, structuring or cutting, which often have extremely challenging requirements on precision and speed. Here, laser scan processes are superior to other methods, e.g. in terms of dynamics and the processing flexibility of complex patterns or structures. The spectrum of processed materials ranges from plastics to glass to ceramics and all the way to diverse metals.
High-performance scanning solutions enable short process times, high dynamics and high precision even for moving workpieces (on-the-fly) as well as workpiece position detection and autonomous scan system tracking for further processing.
Microdrilling
Due to the challenging requirements of microdrilling, special application-specific scan systems are often needed. 'Jump and shoot' applications, such as drilling microvias in circuit boards or solar cells (metal-wrap-through or emitter-wrap-through), require scan systems that provide maximum throughput with the highest precision.
Drilling of injection nozzles requires a scan solution for high-precision fabrication of freely-defined geometries. The precSYS enables fabrication of ultra-fine positively/negatively conical or ideal cylinders and round or elliptical bore holes with high aspect ratios (≥ 10:1). Typical accuracy requirements are in the sub 10 µm range.
Microengraving
Microengraving enables the fabrication of extra-fine structures such as two-dimensional stamp keys and medallion keyways or three-dimensional cast molds. Furthermore, deep-engraving often takes several hours and so the 2D, 2.5 D or 3D scan systems must also exhibit minimal drift while retaining high precision and dynamics.
Microcutting
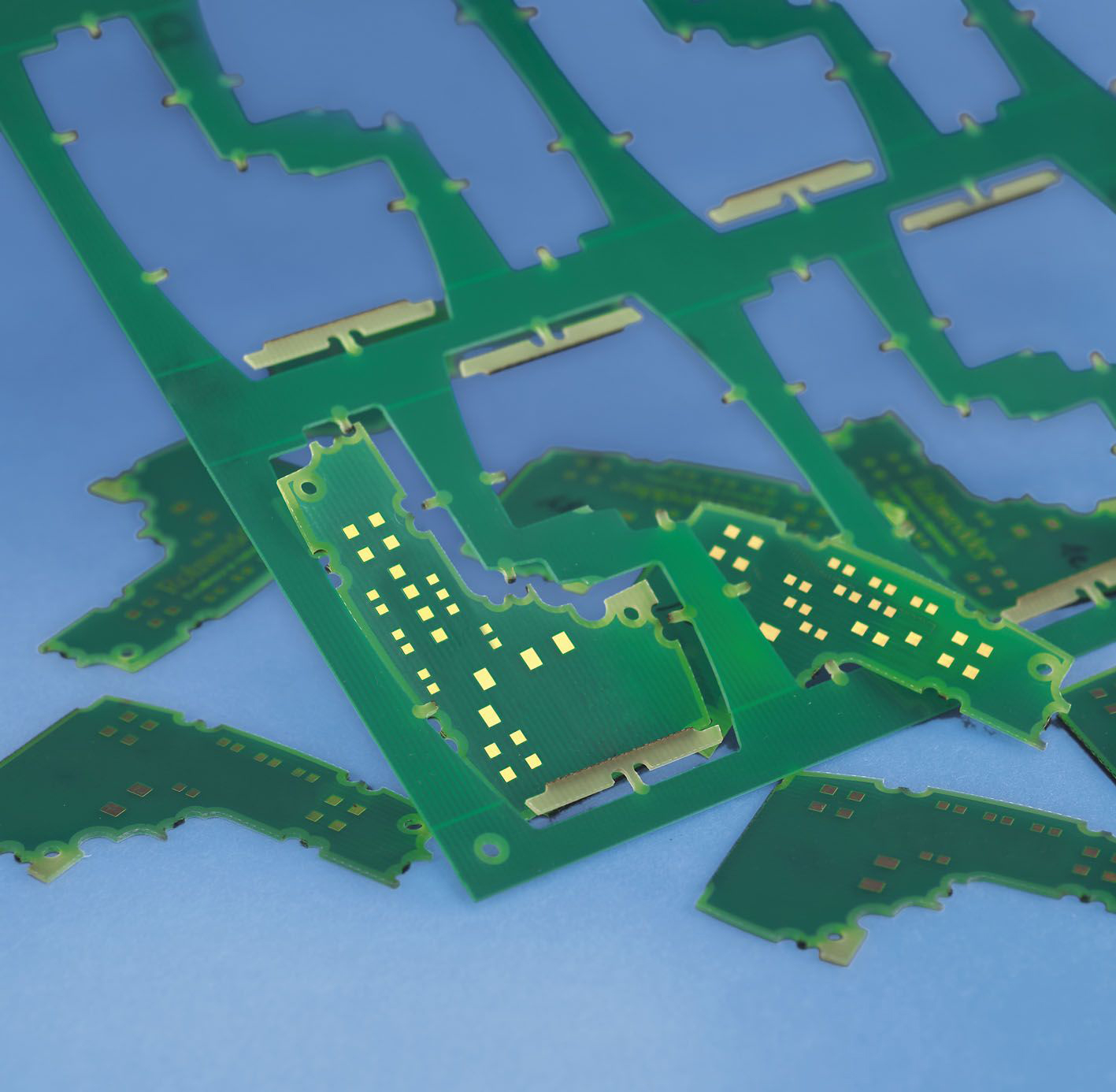
For microcutting capable scan systems transform the laser into a seasoned tool able to cut ultra-fine structures with tight radii quickly, precisely and without the requirement of post-processing.
In conjunction with USP lasers, the effectively simultaneous execution of multiple processing steps is possible. The desired contours are scanned very quickly, often and with high repeatability, without thermal input into the material.
Microcutting is typically applied to materials such as hardened glass, diamond, sapphire glass (corundum), gorilla glass, ceramics, memory metals and PCB materials.
Microstructuring
Surface microstructuring can modify a part's properties. For example, it can be given an electronic function, a lotus effect, slip resistance or leather-like surfaces of injection molds and plastic. In order to economically create these structures even on large surfaces, scan systems are used for fast and precise positioning the laser beam.
Extreme challenges must be met to cost-efficiently process metal or plastic parts with the lotus effect, thin-film solar cells (roll-to-roll process), displays or smart devices. For such applications, ultra-low-drift high-end scan systems are often needed.
Microsintering
The scan system requirements for microsintering are similar to those for deep engraving: minimal drift, utmost precision and fast dynamics.
High-performance scan systems enable the fabrication of high-precision metal functional parts used in the medical technology, aerospace, watchmaking and automotive industry.
Microprocessing with Lowest Dither and 20-Bit Resolution
Synchronous control of the laser and scan system is essential for the best processing results. In addition to an a high perfomance scan system, high positioning control resolution is also needed.
The widely used XY2-100 protocol with only 16-bit positioning resolution is often no longer adequate for micro-machining. Here, the 20-bit SL2-100 protocol, developed and introduced by SCANLAB, is a necessary upgrade. High-end scan systems and control boards such as RTC5 and RTC6 support this protocol.
RTC5 and RTC6 Provide Specialized Functionalities
-
Arc command
For decomposing arcs into micro-vectors, while avoiding quantization effects from ultra-fine structures and high speeds -
Automatic laser control
For automatic real-time adjustment of 'laser active' control signals – and thereby laser power – even during the execution of vector and arc commands -
Pulse-picking laser mode & output synchronization
For straightforward synchronous control of scan systems to an externally clocked free-running pulsed laser (e.g. USP laser). -
Sky-writing
For perfect corners with a minimal increase in process time thanks to a time-optimized implementation
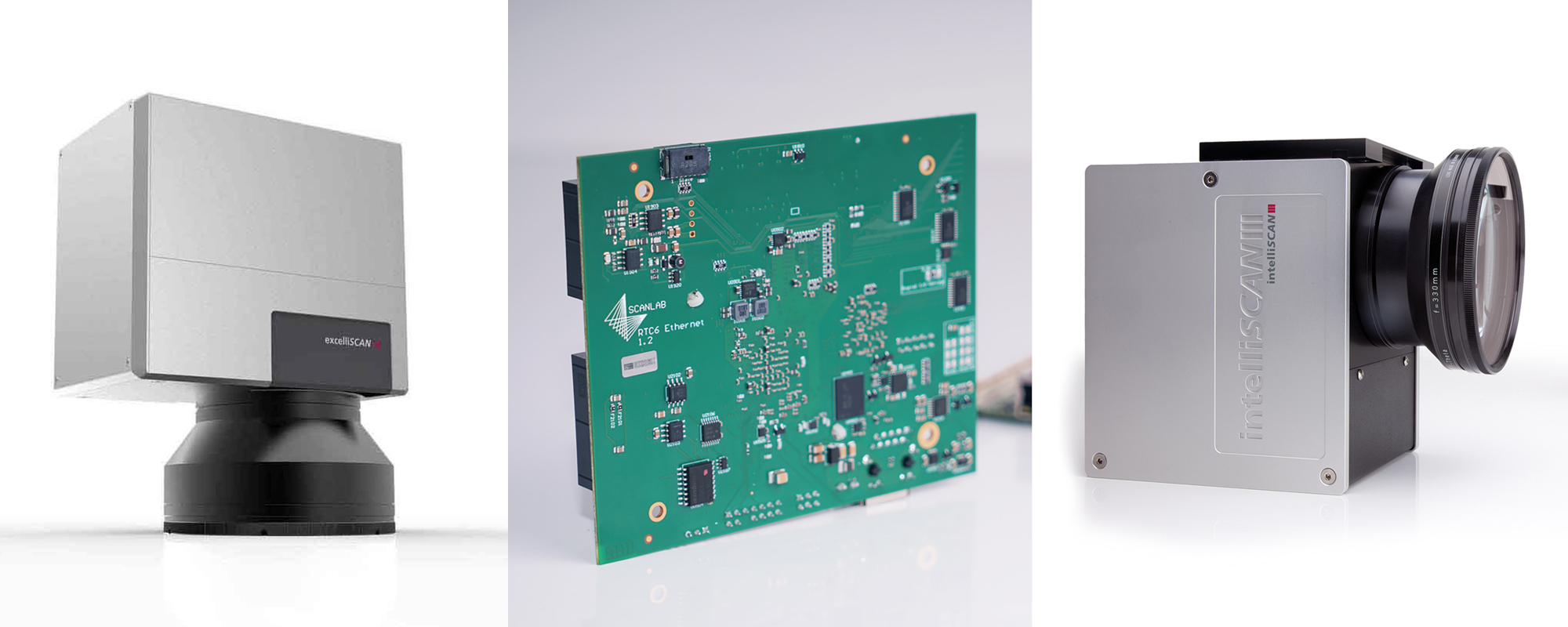
Suitable Solutions
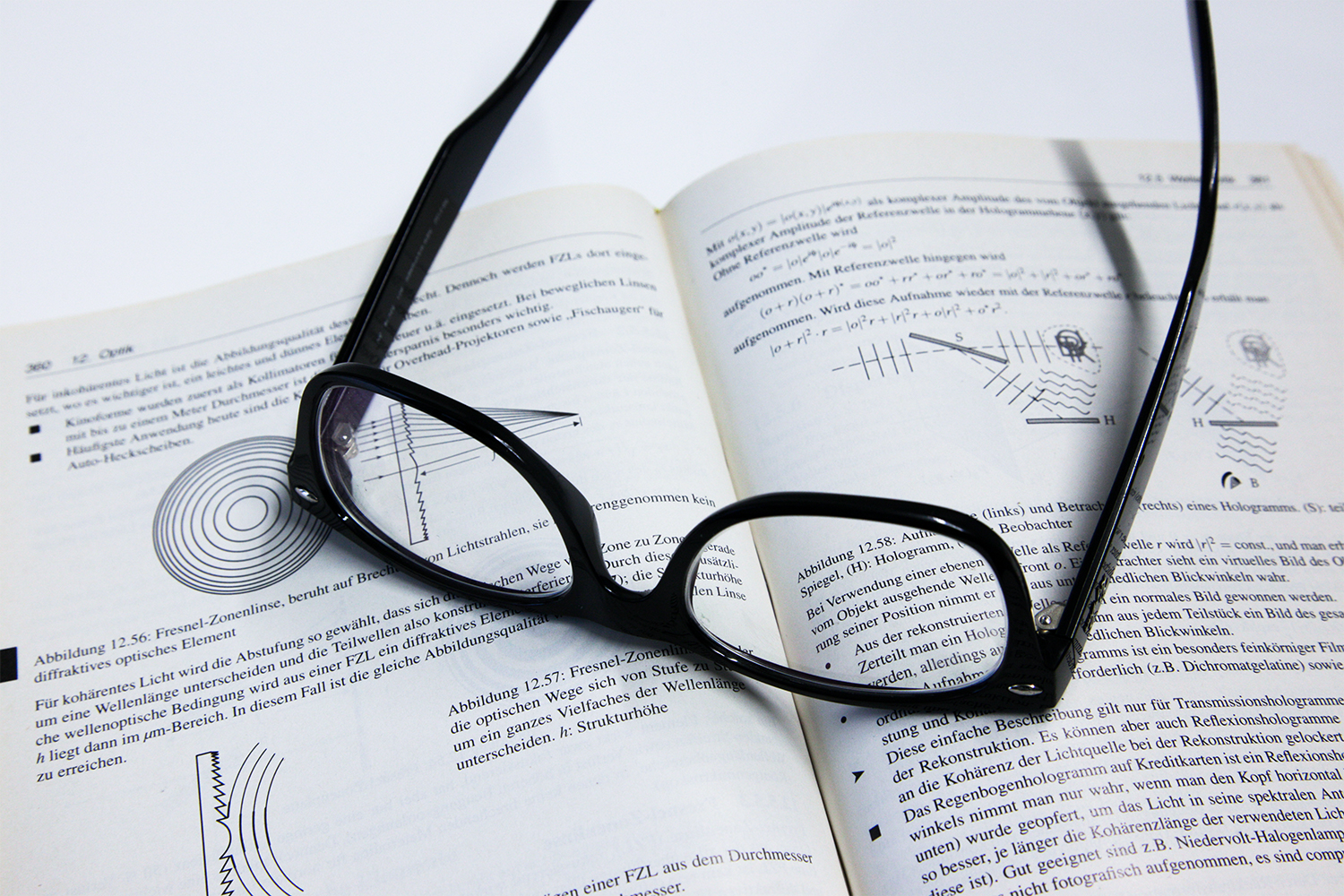
Research Collaborations
DPP Campus (2020-2025)
Investigation of promising next generation scanning technologies to enhance productivity of laser material processing.
eVerest (2016-2018)
Machines and system technology to efficiently fabricate large 3D mold tools with design surfaces.
Ultralas (2010-2013)
High-resolution, ultra-high-speed laser processing system for mass producing photovoltaics.
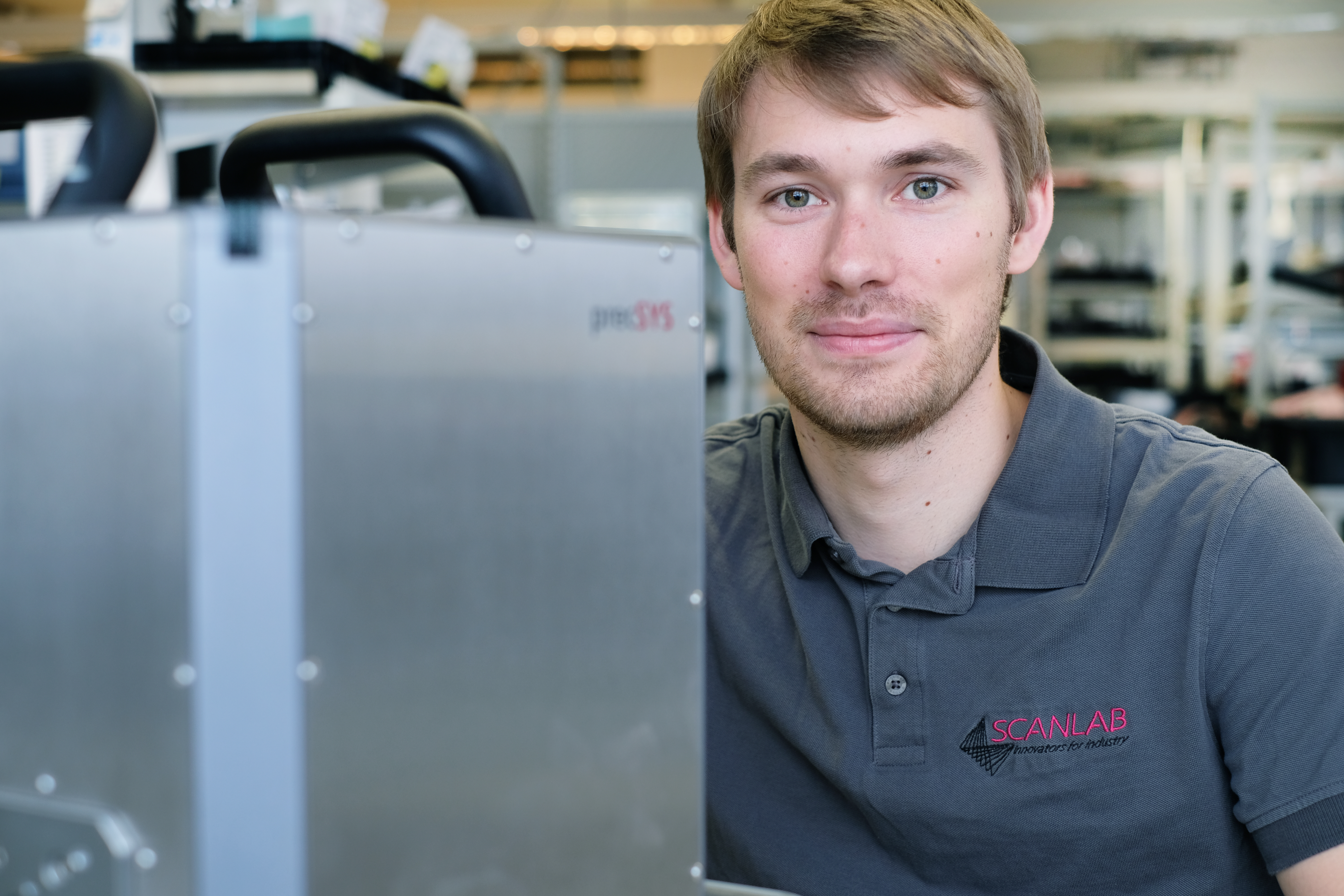
Laser Applications Freely Cross Industrial Boundaries
Laser processing methods are employed in numerous industries. Click a specific industry link to see a selection of processing methods that use galvanometer scanners.