End-to-end software chain for better LPBF machining results
SCANLAB GmbH helps mechanical engineers to develop new metal 3D-printing systems by providing harmonious solution modules. These include high-quality laser scan systems as well as control solutions for efficient laser process development and effective production. Ultra-precise printing results from the Fraunhofer ILT, which can be deployed on industrial machines using the new SCANmotionControl software, will be presented at formnext in Frankfurt. Partnering up with well-known software manufacturers ensures seamless integration of the control solution.
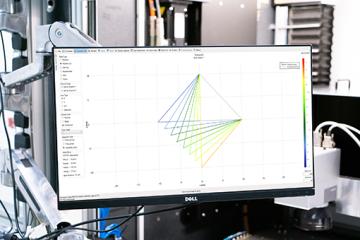
At the heart of laser powder bed fusion (LPBF) machines for 3D printing of metal are the scan systems and their interaction with the laser. SCANLAB has been a pioneer in the development of scan heads for 3D printing since the 1990s. Alongside the hardware components themselves, control systems have become increasingly important in recent years.
Efficient operation of industrial laser machines in the field of additive manufacturing requires control solutions that map the entire software landscape from CAD/CAM to machine software right through to laser job execution. SCANLAB works with leading providers including AUTODESK, DYNDRITE, as well as SIEMENS in combination with AIXPATH, to deliver harmonious solution modules to integrators. This simplifies system development and significantly shortens the time to market for new laser processing machines.
More flexible laser process control and higher component quality
SCANmotionControl, the recently launched control software, makes it possible to synchronize the scan system, laser and other peripheral equipment. The software calculates optimal trajectories for laser machining on the basis of predefined machining patterns and process parameters, taking into account the physical limits of the scan head. The energy input can be defined precisely, since speed and laser power are planned, simulated and adjusted synchronously. Until now, the exact scan path had to be determined through experimentation. Thanks to the offline simulation of the trajectories, this can now be examined and optimized beforehand on the computer. This gives the process developer full control over the energy input at any position on the workpiece. This makes job planning far simpler and makes development times significantly shorter.
Furthermore, by testing the software in additive manufacturing, the experts at Fraunhofer ILT have demonstrated that it is possible to drastically improve the dimensional accuracy of filigree components. "With the use of SCANmotionControl, for example, we were able to avoid edge bulging on complex components – and not just in the lab. Using the software, the results can easily be applied to an industrial scale," explains Dr. Tobias Pichler, Process & Systems Engineering, Fraunhofer Institute for Laser Technology ILT.
The new software allows users to achieve optimum machining results with minimum laser-off times. The scan systems fiberSYS, excelliSCAN and intelliSCAN IV are ready for SCANmotionControl. By working together with the different software providers, the seamless integration of high-quality components into laser machining systems is ensured.