Viewing a Weld Seam in 360°
At the Laser World of Photonics tradeshow in Munich, Germany, Blackbird Robotersysteme GmbH (acknowledged remote welding expert and SCANLAB GmbH associate company) will present an entirely new scan solution prototype with integrated distance sensor. Based on optical coherence tomography (OCT), the system detects and measures 3D laser weld seam topographies in high resolution. This is particularly advantageous for industrial system integrators and users looking to secure process safety and comprehensive quality management without a separate monitoring solution.
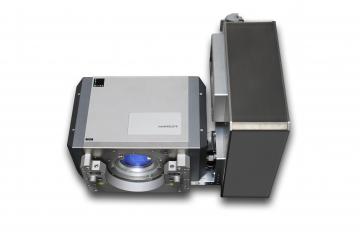
In healthcare OCT has proven itself as an examination technique for opththamology, skin analysis, cancer diagnosis and more. For patients, this optical measurement method is painless and noninvasive. But this form of contactless, interferometric measurement also offers considerable potential to industry.
At Munich's Laser World of Photonics 2017 in June, Blackbird Robotersysteme is presenting a new scan solution with integrated OCT-based edge tracking and seam topology measurement. In contrast to other sensors or measurement methods, this OCT-based distance measuring offers full flexibility by capturing and analyzing detailed data within and beyond the actual laser processing zone. For example, this includes analysis of to-be-welded components, seam tracking of fillet welds and real time detection of any weld errors or imperfections occurring during weld operations.
Here, the OCT sensor's measuring light is coaxially coupled in a laser weld head's beam path and then guided together with the laser beam via the weld head's main mirrors. Monitoring thus always takes place directly within the process zone – thereby inherently avoiding contour following limitations that occur to some extent in lateral monitoring solutions. Moreover, the measuring beam has a scan system of its own that enables positioning all around the processing point. The integrated high-quality sensor and finelycoordinated calibration between the OCT scanner and laser scan system all team up to ensure high scanning frequencies and measurement accuracy between the scan head and to-be-welded components. This permits a detailed three-dimensional representation of the weld seam for unequivocal quality assurance.
"This new system affirms our strategy of offering complete laser welding solutions with integrated seam tracking and profile analysis," explains Thibault Bautze, Sales Manager at Blackbird Robotersysteme GmbH. "For our customers, this is a further step toward simplifying and visualizing weld processes, avoiding interfaces and increasing production quality – as evidenced by the first highly promising test trials. All components are perfectly matched and supplied from a single source. The underlying control electronics from SCANLAB allows synchronization of seven axes with high precision. The result makes us clearly stand out from other systems in terms of working fields, speed and precision."
Blackbird's system solutions offer custom interfaces for all leading robot systems, such as ABB, Comau, FANUC, Kawasaki, KUKA or YASKAWA, and find use worldwide in industrial manufacturing, particularly motor vehicle production. The first test systems with the new, integrated OCT solution will be installed in 2017. The scope of delivery includes the scan optics and control system, as well as the complete software architecture with intuitive graphical user interface.